Cost of Quality
- Hello
- Post right sidebar
- 23 November 2022
- By Akshay P
- 0 Comments
In this article let’s understand the cost of quality and how it impacts on the business front.
What are Quality costs?
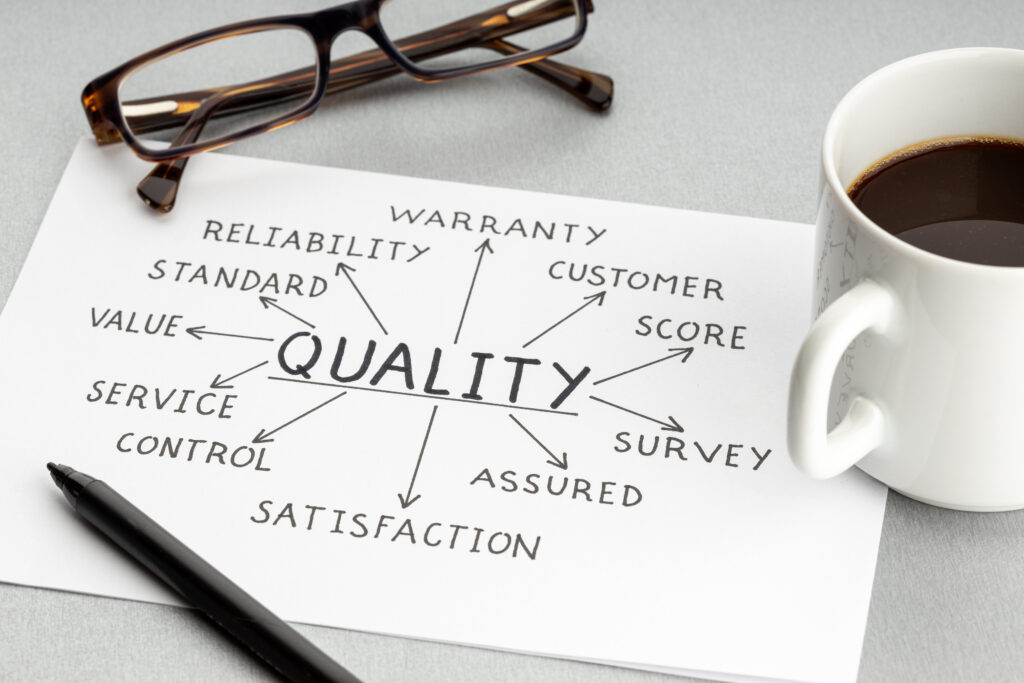
Quality costs are the costs associated with preventing and detecting product issues related to quality. Quality costs do not involve simply upgrading the perceived value of a product to a higher standard. Instead, quality involves creating and delivering a product that meets the expectations of a customer. Thus, if a customer spends very little for an automobile, they will not expect leather seats and air conditioning – but will expect the vehicle to run properly. In this case, quality is determined by the function of the vehicle , rather than an experience of luxury.
Product quality refers to how well a product satisfies customer needs and serves its purpose. When evaluating product quality, businesses consider several factors, including whether a product solves a problem, works efficiently, etc.
Why should we speak about Quality?
It’s because it improves our products and business operations, which leads to a stronger market position. Quality management can enhance our organization’s brand and reputation, protect it against risks, increase its efficiency, boost its profits, and position it to grow.
Let’s take an example: Everyone at least once would have gone shopping. Have you ever compromised on the quality of clothes and bought torn clothes? I believe you would never purchase such things! Then why are you forcing your customer to purchase, buy, or accept such products? They are also paying you for this! This will ensure trust building with our customers!
Have you ever gone back to the same place from where you bought faulty products or low quality items? In the same light, customers won’t come back to us either if we don’t deliver good quality products.
Who is responsible for Quality?
Quality is everyone’s responsibility. Everyone in the organization should be responsible for quality. Different people will have responsibility or influence over different things that affect quality, such as designing the UI, specifying requirements, meeting those requirements and determining the quality. Quality is not a one time activity, it is a continuous process. It is not the result of efforts from a single person, but a team’s effort.
Now let’s go through the types of cost of quality
Imagine if you are a user/buyer. Which kind of product would you choose? The answer would be a product of good quality. Because we don’t want to pay the cost for the product which would yield poor quality.

Let’s see what are the costs of poor quality
- Internal failure
- External failure
Internal failure costs are costs that are caused by products or services not conforming to requirements and are found before delivery of product to external customers. They would have otherwise led to unsatisfied customers. Examples include the costs for: Rework, Re-designing, Delays, Re-testing, Downgrading, Downtime, Lack of flexibility and adaptability of Employees, etc.
External failure costs are costs that are caused by defects found after the delivery of a product to external customers, which leads to customer dissatisfaction. Examples include the costs for: Customer issues, Redoing designs, Environmental costs, Losses due to sales reductions, etc.
Let’s see what are the costs of Good Quality
- Appraisal costs
- Prevention costs
Appraisal costs are costs that occur because of the need to control products and services to ensure a high-quality level in all stages, conformance to quality standards and performance requirements. Examples include the costs for: code reviews, testing, design audits, product audits, monitoring environments, etc.
Prevention costs are costs of all activities planned and designed before operations to guarantee product quality and prevent bad quality products. Examples include Quality planning, new product review, process reviews, improvement in team meetings, education and training.
How to measure cost of quality?
Cost of quality = Internal failure costs + External failure costs + Prevention costs + Appraisal costs
Hypothetical case evaluation
On account of COQ(Cost of quality) practicality, let’s conduct a small hypothetical case evaluation.
Say, we are developing a mobile app with 2 scenarios: with and without quality management. In each case, we’re dealing with 200 errors (bugs) total, and assume a $20 price to fix a bug found internally, while a $100 price to fix a bug found externally.
First case – no quality management
In the first case, without quality management in place, COQ investment is zero, and we only spend money to fix bugs.
Say, we found 50 bugs internally, and customers reported 150 after they used the app.
Total COQ would equal (50*$20)+(150*$100)= $16,000.
Second case – 100 h for quality management
In the second case, let’s assume we spend 100 additional hours on quality management procedures. Thus, at the average $50 hourly developer rate, we invest about $5,000 in software quality.
As a result, we detect more bugs internally – 175, lower external bugs to 25.
The total COQ equals $5,000+((175*$20)+(25*$100))= $11,000.

As we see, the total cost of quality is in favor of the second case. Although this is neither an ultimate equation and the figures aren’t exact, it’s possible to conclude that if you invest in essential features of a product and you build and ensure real quality there, then COQ in software development is really worth considering.

Above graph shows the relationship between prevention costs and failure costs. X-axis contains ‘Quality level’ and Y-axis contains ‘Quality cost’. For prevention costs i.e the green line, quality level would be low in the beginning and when prevention methods are taken cost would be increased with good quality. For Failure costs i.e orange line, quality level will be high in the beginning but due to failures caused after deployment, quality cost would be increased eventually. So, Cost of quality = Internal failure costs + External failure costs + Prevention costs + Appraisal costs
Why measure the cost of quality?
The determination of the cost of quality remains to be critical and varies for different organizations. If this cost is not measured and quantified, organizations working in the competitive industries would never gain the upper hand and survive the ever-changing dynamic environment. Therefore, measuring it is necessary as it helps the business maintain a healthy and positive bottom line.
Best practices when trying to lower your COPQ
- Start with product design and development. Since customer expectations define quality, quality begins with product development and design. How well does your product’s design match what the target consumer is looking for? Sometimes companies experience quality issues and then naively assume their quality is at fault. Upon digging deeper, we find the problem lies in how the company designed the product. If a product’s design is flawed, to begin with, it doesn’t matter how well the factory produces it. You need to ensure that the design, dimensions, components, and all relevant details are optimized to meet consumer expectations.
- Always remember that while quality initiatives will minimize your defects, it’s rare to reach zero defects over time. Be sure to put the right processes in place that help identify the error as early as possible. These additional verification steps have a cost, but the cost should be far less than the cost of the error going undetected until later.
- If a new product has been moved into production too soon and is experiencing multiple or critical defective issues take immediate action to assign the personnel needed to address the issues before moving on to future projects. Otherwise, you are taking a large risk regarding repair costs and the reputation of your customers.
Benefits
The cost of quality helps the business derive a competitive edge over its peers working in the industry. It allows the organization to plan for costs that the business has to incur in maintaining quality costs and helps the organization make provisions for them, which helps the organization maintain a favorable bottom line.
Conclusion
The cost of quality can be termed as the costs the business has to bear to utilize its resources to maintain qualitative outputs to its targeted customers. If the business does not employ its resources to adhere to quality metrics, it will lose out on its competitive advantage. Furthermore, if the cost of quality is not incorporated, it can severely impact the business’s bottom line.
0 Comments